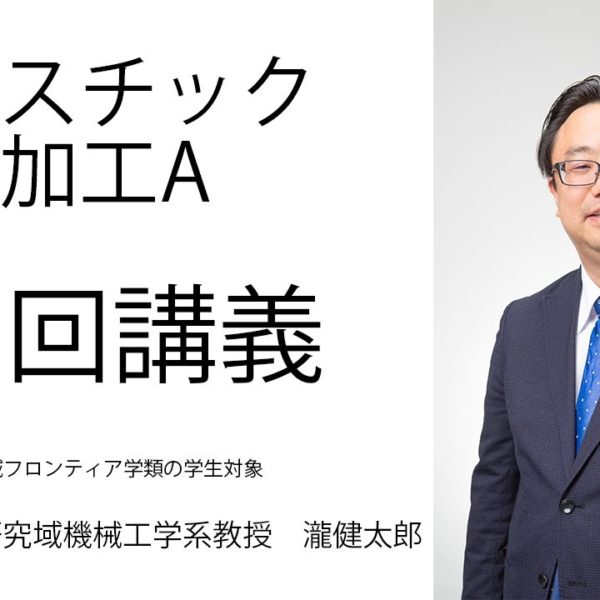
フリーブロー成形
プラスチック・樹脂加工の一つであるパイプ押出し成形は、熱可塑性樹脂材料を連続的に成形することで、管状の製品を作成する加工技術です。この製法は、建築・建設、自動車、水道、ガスなど幅広い産業で使用されるパイプやホースを製造するために広く利用されています。
プロセスは以下のステップで行われます。
🔵原料準備: 樹脂ペレットを乾燥させ、適切な湿度に保ちます。乾燥により、樹脂内の水分が取り除かれ、押出し成形品質が向上します。
🔵樹脂加熱: 乾燥した樹脂ペレットを押出し機のバレル内で加熱し、熱可塑性状態にします。このバレル内には、スクリューが設置されており、樹脂を加熱しながら前方に押し出す役割を果たします。
🔵パイプ成形: 加熱された樹脂がバレルの先端から射出されると、ダイと呼ばれる金型を通過します。この金型は、製品の外径、内径、厚みなどの形状を決定します。
🔵冷却・固化: 押出されたパイプは、冷却装置(水冷却槽や空冷ファン)を使用して冷却・固化させます。これにより、樹脂が安定した形状を維持できるようになります。
🔵切断・検査: 冷却・固化したパイプは、所定の長さに切断され、最終製品として検査されます。寸法、外観、物性などの基準に合格したものが出荷されます。
このように、パイプ押出し成形は、製造工程が単純であることから生産性が高く、様々な樹脂材料を用いてカスタマイズされたパイプ製品を作ることができます。
会員でない方は会員登録してください。