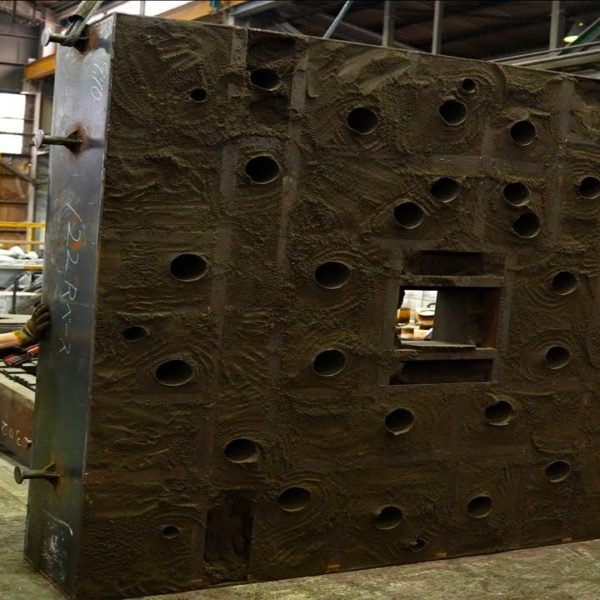
冷間鍛造
冷間鍛造とは、加工材料を加熱せず、常温状態で行われる鍛造加工の一種であり、製造業において自動車、航空、建設機械、電子部品等の生産に広く用いられています。高い寸法精度、良好な表面品質、緻密な組織構造が特徴で、材料の機械的特性向上や製品の寿命を延ばす効果が期待されています。
冷間鍛造の加工ポイントは以下の通りです。
🔵材料選定: 冷間鍛造に適した材料は、低温での延性と靭性が良好で、加工硬化現象に対して適度な感受性を持つものが望ましいです。例えば、炭素鋼、合金鋼、アルミニウム合金、銅合金などが適しています。
🔵加工方法: 冷間鍛造では、打ち抜き、押出し、圧延、曲げ、折り曲げ等の加工方法があります。製品の形状や用途に応じて、適切な加工方法を選択することが重要です。
🔵金型設計: 冷間鍛造では、金型の寸法精度や表面仕上げが製品品質に直接影響を与えます。適切な金型設計は、鍛造時の材料流れや加工硬化を考慮し、成形後の材料の応力分布や寸法精度を最適化することが求められます。
🔵潤滑剤の選択: 冷間鍛造では、適切な潤滑剤の選択が摩擦抵抗の低減や型寿命の延長に役立ちます。潤滑剤は、金型と材料の相互作用を考慮し、最適な膜厚や滑り性能を持つものを選択することが重要です。
🔵加工速度: 加工速度は、冷間鍛造における力学的特性や表面品質に影響を与えます。適切な加工速度は、材料の応力状態や加工硬化を考慮し、適切な範囲内で設定することが求められます
冷間鍛造後の熱処理: 冷間鍛造による加工硬化を緩和し、材料の機械的特性を向上させるために、適切な熱処理が必要です。焼入れ、焼戻し、アニーリング等の熱処理方法を選択し、材料の特性や用途に合わせた最適な状態を得ることが重要です。
🔵製造コストの最適化: 冷間鍛造は、一般的に高い寸法精度や良好な表面品質を得ることができますが、金型や機械設備のコストが高いため、製造コストの最適化が課題となります。プロセスの効率化や材料使用率の向上、金型寿命の延長等を通じて、製造コストを最適化することが求められます。
これらの加工ポイントを適切に管理することで、冷間鍛造による高品質な製品の製造が可能となります。製造業においては、冷間鍛造技術の研究開発や技術者の育成が、競争力向上や製品の付加価値向上に貢献することが期待されています。
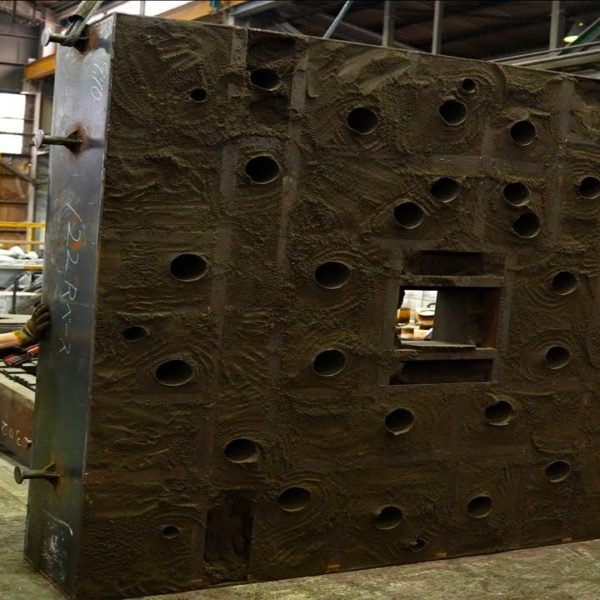
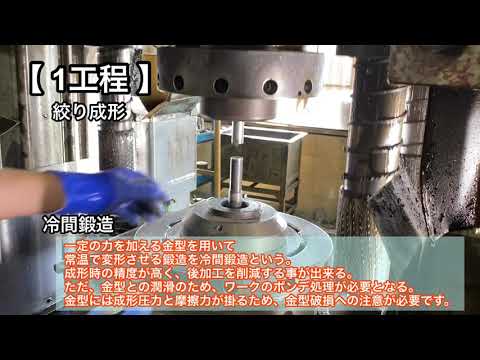
【冷間鍛造】スプライン成形
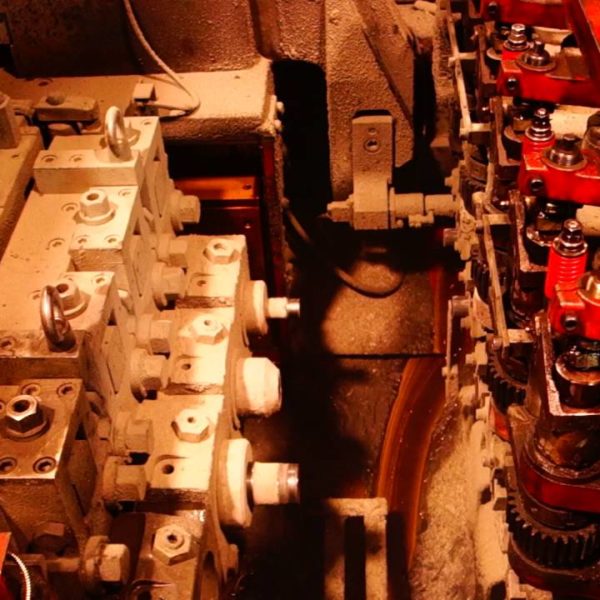
フォーマー機SF600による冷間鍛造 (cold forging)
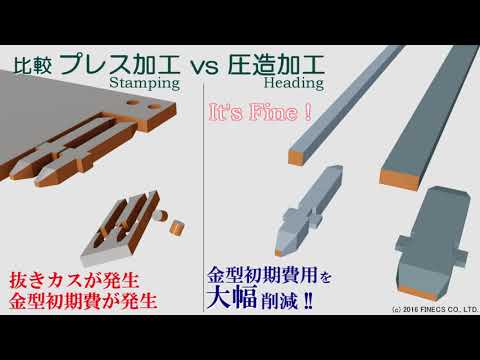
線材圧造ヘッダー加工と条材プレス加工の比較
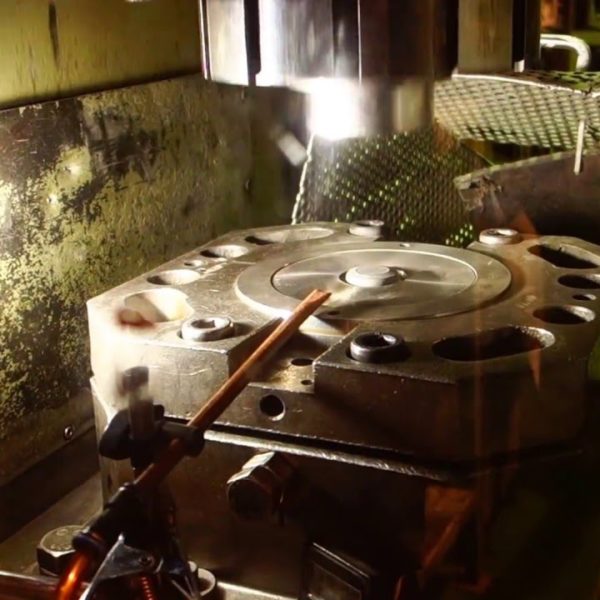
手動300Tプレス機による冷間鍛造 (cold forging)
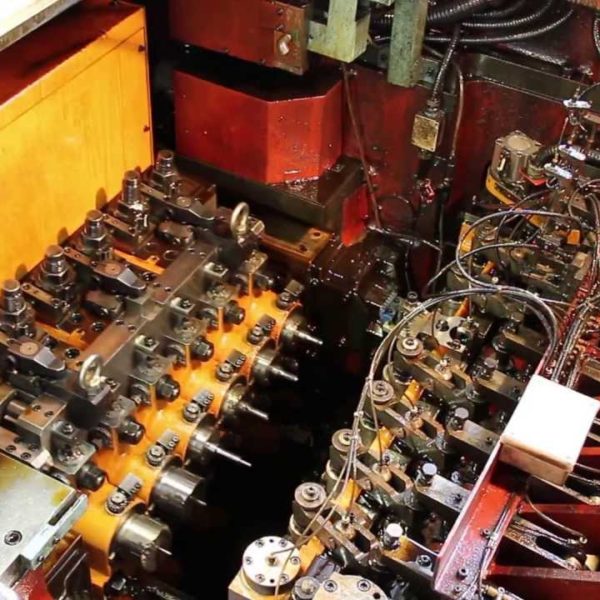
冷間圧造/(株)石渡螺子製作所
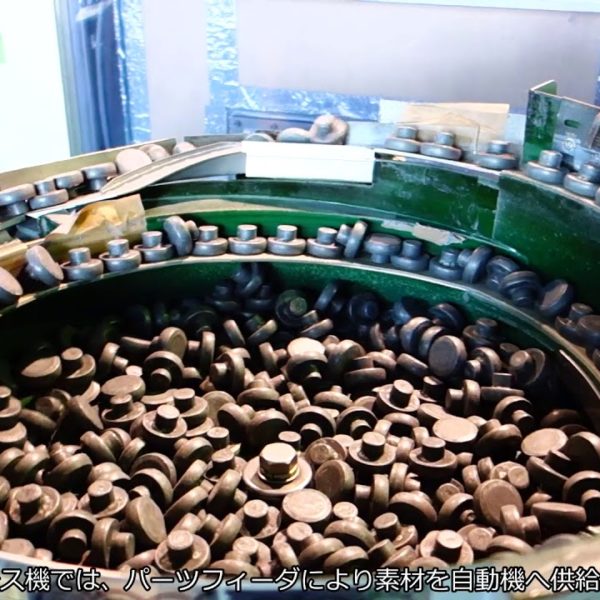
【上板塑性】冷間鍛造によるものづくり(long ver.)
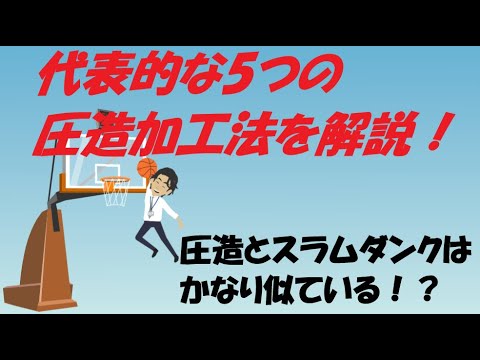
代表的な5つの冷間圧造(冷間鍛造)加工法を分かりやすく初歩解説!
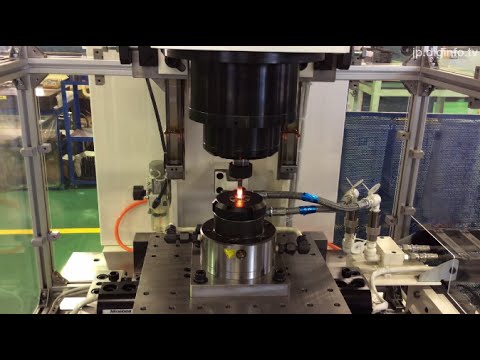
【高強度部品】高強度ステンレスの冷間鍛造成形技術が凄い!
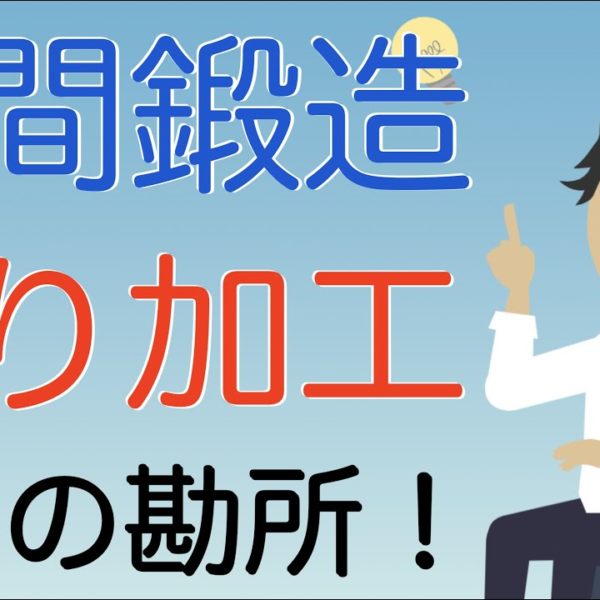
冷間鍛造 絞り加工の勘所を解説
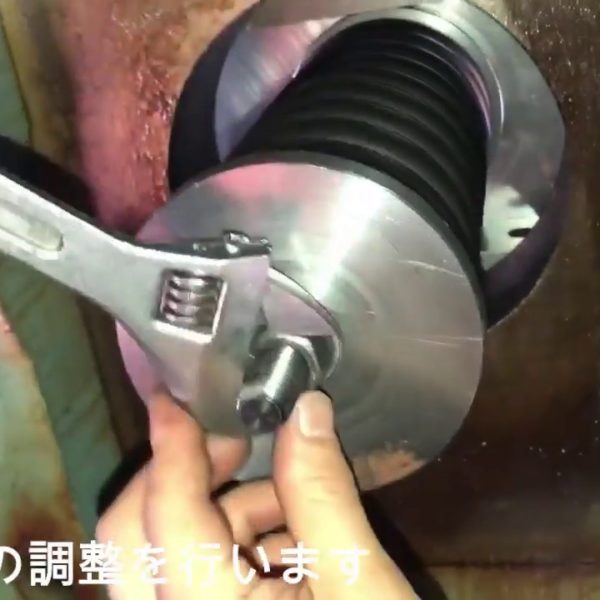
金属プレス 随時3級 検定指導 ダイジェスト
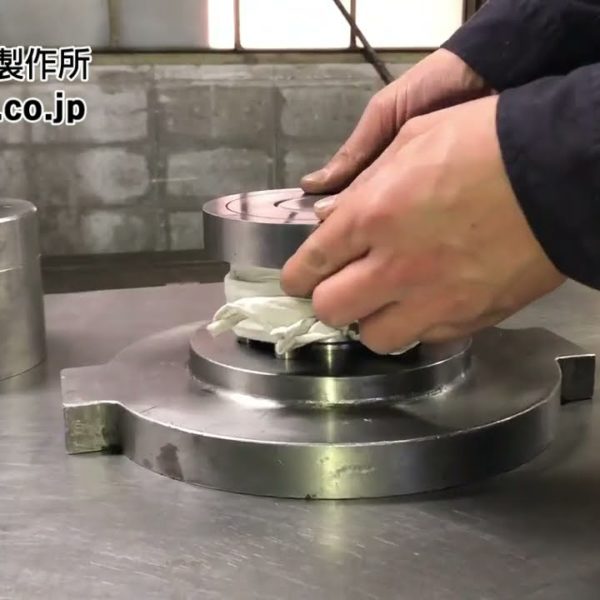